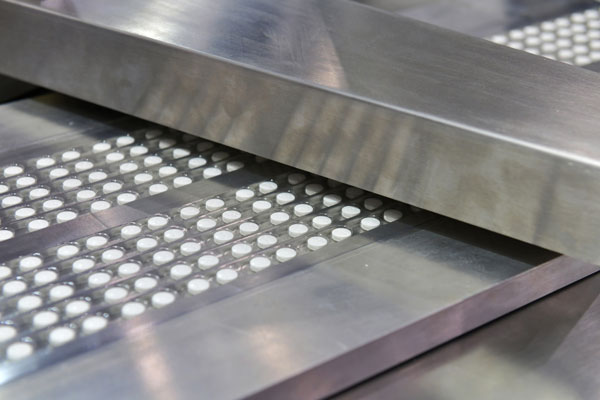
アステラス製薬がデータサイエンスを駆使してものづくりの高度化を図っています。製造現場のデータを収集・解析するデータマイニングシステム「DAIMON」を自社開発。膨大なデータをモニタリングすることで、品質や生産のトラブルに備える仕組みを構築しています。
3つのモニタリングをリスクに応じて運用
2021~25年度の経営計画で、▽抗がん剤「XTANDI」と重点戦略製品で1.2兆円以上の売り上げ(25年度)▽フォーカスエリア・プロジェクトから5000億円以上の売り上げ(30年度)▽コア営業利益率30%以上(25年度)――を通じて25年度に株式時価総額を7兆円以上に引き上げることを目指しているアステラス製薬。目標達成の要の1つにデジタルトランスフォーメーション(DX)を位置付け、研究から開発、製造、営業までバリューチェーン全体を通してDXを推し進めています。
関連記事:アステラス、営業効率化へ大なた…グローバルで1000人削減 DXで生産性向上
中でも比較的早くから取り組んでいるのが、データサイエンスを駆使した高効率かつ高品質なものづくり。製造現場のデータを収集・解析するデータマイニングシステム「DAIMON(=Data Analysis and Integration for Multivariate mONitoring)」を自社開発し、2018年から稼働しています。DAIMONは、生産工程でリアルタイムに収集した大量のデータをモニタリングすることで、製品と生産プロセスの理解を深め、将来の品質/生産トラブルを未然に防ぐのをサポートするシステムです。
DAIMONは▽統合基幹業務システム(ERP)▽製造実行システム(MES)▽ラボ情報管理システム(LIMS)――などから得られるデータと、環境モニタリングや製造機器などの稼働データなどを自動で収集。「一変量モニタリング」「因果・回帰関係モニタリング」「多変量モニタリング」という3つのモニタリングをリスクに応じて運用し、トラブルの原因調査や潜在リスクの把握、変動検出などに役立てています。
「生産段階に入っても理解を深め続ける必要がある」
一変量モニタリングは、いわゆる統計的プロセス管理を指します。1ロットあたり数千におよぶデータをもとに、トレンドモニタリングで品質のばらつきを分析・管理。ウエスタンエレクトリックルールに基づいた異常検知でトレンド異常を見逃さない仕組みを作っています。因果・回帰関係モニタリングは、研究開発段階で見出された因果・回帰関係のモデルが生産段階で維持されているかを確認するもの。たとえば、錠剤の溶けやすさを把握するために、粒子の大きさと錠剤の硬さの関係をモニタリングします。
一方、多変量モニタリングでは、生産段階のビッグデータから多変量モデルを構築。信頼区間を設定し、生産ロットがそこから外れていないかをチェックします。外れたロットについては、どのパラメータが変動に関与したかを確認することができるため、迅速な対応が可能になるとともに、製品と生産プロセスに関する理解を深めることにつながります。
「われわれは開発段階で十分に製品とプロセスへの理解を深めてから医薬品を発売していますが、生産段階でさまざまな変動に遭遇することは避けられません。それが結果的に品質/生産トラブルにつながっているのが実態です。生産段階でも製品とプロセスへの理解を深めながらものづくりの技術を高度化する必要があり、データマイニングを取り入れました」
DAIMONを担当する製薬技術本部製剤研究所プロセス設計研究室の則岡正さんは、システムの意義についてこう説明。「品質問題は、患者の健康や安定供給だけでなく、社会的信頼の損失にもつながるため、プロアクティブな対応が重要です」と話します。
データ駆使しプロアクティブに対応
2011年には着想を得て、2015年から開発を進めてきたDAIMON。1つの製品で数千のパラメータを扱うため、18年の稼働開始以降、低分子化合物からリスクベースで製品を選んで展開を進めてきましたが、21年からはバイオ医薬品でも活用を始めました。
DAIMONを導入する前は、品質担保に関連するデータの管理はほとんど紙ベースで行っていたというアステラス。トラブルの原因は複雑であるにもかかわらず、データが散在していたため、管理や解析に多くの時間がかかっていたといいます。「トラブルが発生してしまうと、CAPA(是正処置および予防措置)の適用やそれに伴う一変申請など、当局への説明が別途必要になることもあり、従来は対応に数年かかっていました」と則岡さん。「これから起こることを未然に防ぐということはなかなかできていなかった」と振り返ります。
実際の活用事例は
実際、アステラスはDAIMONをどのように活用しているのでしょうか。
製造現場の社員は日々、DAIMONを使って気になる製品のトレンド変化などを確認し、朝礼などの場で気づきを共有。製品への理解を深めるのが狙いです。DAIMONを扱うための基礎的な統計リテラシーを学ぶ研修カリキュラムも用意されています。
則岡さんは、トラブルの未然防止や生産プロセスの改善などに繋がったケースとして、特にインパクトが大きかった3つの事例を教えてくれました。
(1)トレンド異常の原因特定(低分子医薬品)
国内で製造する錠剤で、製品の定量値(有効成分が規定量に対して何%入っているか)にトレンド異常を検出したあと、すぐに原因を特定できたケースがあったといいます。異常のあったロットについて、DAIMONを使って数千のパラメータの相関関係を上位から10項目調べたところ、原薬の定量値と製品の定量値に負の相関があることをキャッチ。原薬の定量値にばらつきがあり、定量値補正(製品の定量値が規定の100%になるよう原薬の仕込み量を調節すること)がうまく機能していないことを突き止めました。
(2)生産プロセスの改善(バイオ医薬品)
国内で扱うあるバイオ医薬品で、ロット間でばらつきのあるプロセスを改善しました。このケースで見直したのは、A液をB液に変換する作業工程。作成されたB液にばらつきが生まれることで追加の調整作業が発生してしまい、残業につながっていることが課題でした。現場では、関連するデータをDAIMONで確認し、A液に紐づくパラメータYとB液に紐づくパラメータZに高い相関があることを発見。パラメータYに基づき、追加作業の有無を予測することができるようになったといいます。
ここで見出された相関は、研究開発段階にはわかっていなかった未知の関係。「われわれ専門家の観点からすると、なるほどと思える妥当な相関関係でした」と則岡さんは振り返ります。数千のデータがある以上、すべての因果関係を研究開発段階で理解するのは不可能です。網羅的なデータ解析によって、気づけなかった関係を見つけ、プロセスの改善にもつなげることができた事例だと話しました。
(3)製品と生産プロセスの深化(低分子医薬品)
海外の低分子医薬品製造でも、未知の関係を把握できたことで生産プロセスの理解が深まった事例があったといいます。このケースでは、錠剤の溶出に関連する既知の因果関係のモニタリングで異常を検知。データサイエンスチームと連携し、DAIMONに蓄積された350ロットほどのデータを使って高度な解析を行い、新たな関係を見出しました。これを考慮した新しい多変量モデルをDAIMONに取り込み、継続的にモニタリングを行っています。
※※※
DAIMONは、こうした知識獲得のサイクルを、人の手をあまりかけずに効率的に回すことができるツール。2019年には、低分子化合物の生産で提携するCMOへの展開も始めました。日々使っていくことで、社員一人ひとりの品質への感度の向上につながっていると則岡さんは話します。
将来的には細胞医薬などの新規モダリティにも応用し、未来のものづくりを実現する技術としてさらに展開させたい考えです。