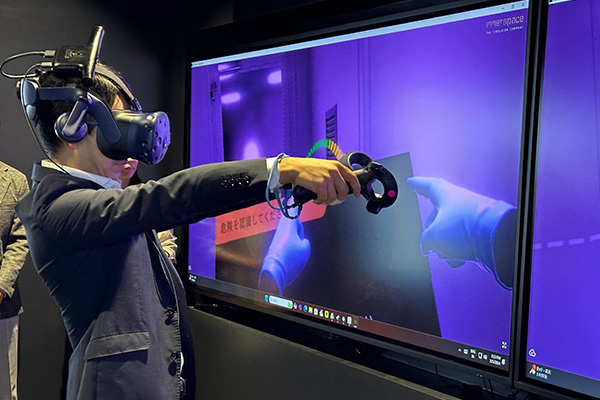
無菌室での動きをトレーニングするVR研修プログラムのデモ
武田薬品工業が2018年ごろから取り組んでいる製造現場のDX(デジタルトランスフォーメーション)が成果を上げ始めています。データとテクノロジーを駆使して自動化・効率化を進め、生産性を向上。日本だけで2022年度に5万時間、23年度に11万時間の作業時間を削減しました。同社は「人がより創造的な活動に注力できる環境を作り、ひいては医薬品を安定的・スピーディに供給することを目指す」としています。
VRで無菌環境再現、研修に活用
「VRやARを使った新しい学習、ロボットが当たり前にいる製造ライン。そこで働く従業員はこれまで以上に創造的で付加価値の高い業務にフォーカスする。武田はそんな未来の工場の形を目指している」
武田薬品は今月5日、製造部門のDXに関するメディア向け説明会を開き、グローバルマニュファクチャリング&サプライ/グローバルクオリティデータ デジタル&テクノロジーヘッドの石丸宏氏は工場の目指す姿についてこう語りました。
石丸氏が言う「新しい学習」の一例が、無菌環境で作業を行う従業員を対象に行っているVRを使ったトレーニングプログラムです。VR空間に実環境を再現することでトレーニングの場所・時間の制約がなくなった上、直感的で理解しやすくなり、過去2年半でトレーニング時間を1万時間以上削減しました。当初は初期の訓練のサポートツールとして導入しましたが、今年からはGMP教育に組み込んでいます。
無菌環境での動作の速度を習得するトレーニング。「無菌室では菌を巻き上げないようにゆっくり動く(1秒間に30~40㎝程度)必要があるが、マニュアルを読んでもピンとこない」(石丸氏)。VRを使ったトレーニングでは、ヘッドセットに埋め込まれたセンサーが受講者の動きを検知してタイムリーにフィードバックする
武田の製造サイトは世界に25以上あり、各拠点が各々の機能や製造品目に応じたロードマップに基づいて製造の効率化、安全性の向上、品質・コンプライアンスの強化、付加価値の創造に取り組んでいます。グローバルでは各サイトの取り組みをベストプラクティスに昇華させ、横展開を図ることでイノベーションを後押ししており、同社では一連の取り組みを「Factory of the Future」プログラムと呼んでいます。
ベストプラクティスのノウハウは、社内のマーケットプレイスに蓄積されています。石丸氏は「さながら社内アマゾン」と言い、各サイトはここから自らの課題にマッチするソリューションを探し、時にカスタマイズしながら現場に適用していきます。マーケットプレイスには現時点で180のソリューションが展開されており、このうち12程度が日本発。ソリューションは、製造・品質部門専任のデータサイエンティスト約100人が所属するチームが現場と協力して開発しています。日々新たな課題も吸い上げ、投資対効果や他サイトへの展開可能性も考慮しながらDXを進めています。
データ活用で「予測型工場」
武田は2019年ごろから、各工場の製造・品質データを統合したデータ基盤の整備に取り組んでいます。MES(製造管理システム)やLIMS(品質管理システム)のデータのほか、温度や圧力といった各製造工程の時系列データなどを、加工しやすい形でAWS(アマゾンウェブサービス)のクラウドに集約。リアルタイムで横断的にデータをモニタリングできる環境を整えてきました。こうしたデータの活用で目指すのは、現在のトレンドから未来を予測し、安定的かつ高効率な医薬品生産を行う「予測型工場」。21年以降、利活用が活発化し、取り組みの成果も出てきているといいます。
たとえば、LH-RH誘導体製剤「リュープリン」などを製造する光工場(山口県光市)では、原薬の収量を予測するシミュレーションモデルを開発。2つの製品について原薬収量低下の要因となった作業を特定し、作業手順を標準化することで収量改善につなげました。2つの製品のうち1つでは手動で調節していた冷却水バルブ制御が、もう1つの製品では作業員による原薬投入速度のばらつきが原因として特定されたといいます。
同社グローバルマニュファクチャリング&サプライ ジャパン 戦略企画部データサイエンスグループヘッドの深川俊介氏は、その効果について「従来は、200を超える製造パラメータについて、ラボ実験で個別に収量との関連を検証していたが、予測モデルを使うことで原因特定までの工数が大幅に削減できるようになった」と話します。
説明会に登壇した武田薬品の深川俊介氏(左)と石丸宏氏
光工場で開発したシミュレーションモデルには、同工場で収集した原薬製造工程のビッグデータを活用。データに多変量解析や機械学習を適用するとともに、物理化学の理論モデルを組み合わせることで、計測データが十分でない場合にもクリアな予測結果を導けるモデルを作り上げました。将来的にはリアルタイムの製造データとも結びつけ、現場の作業員へのレコメンデーションや、設備の自動制御などにもつなげていきたい考え。同様の収量改善に向けた取り組みはスイスのヌーシャテル工場でも行われています。
設備保全でも「予測型」への転換が進みます。大阪工場(大阪市)や光工場では、重要機器の集中監視と設備から収集したデータのリアルタイムモニタリングによって、設備異常の予兆を事前に検知できる仕組みを構築しました。大阪工場では、凍結乾燥機に使われる回転機器(真空ポンプなど)に振動センサーを取り付けてモニタリングし、部品の摩耗を早い段階で察知。生産計画に影響することなく部品の交換を行うことができたといいます。設備故障によって逸脱が起こると、製造が遅滞するだけでなく、原因特定と対処に時間を要するため、これを未然に防ぐことで生産性の低下を回避します。
目指すのは無人化ではない
ビッグデータは、環境負荷の低減にも活用されています。大阪工場では、製造機器の洗浄などに使う蒸留水の使用状況をモニタリングし、蒸留水の使用量とその製造に使用する都市ガスを27%削減。削減量は、蒸留水が年間45万L以上(上水200万L以上に相当)、都市ガスが年間7900㎥以上に上ります。
「それまではたびたび、蒸留水が枯渇して製造を続けられなくなることがあり、追加投資して蒸留水の生産量を増やすことも検討していた。しかし、現場の声もあってまずは現状を把握した結果、必要以上に水を使っている工程が判明し、そこを手当てすることで枯渇もなくなった。追加投資も不要となり、大幅なコスト削減につながった」と深川氏は話します。
この取り組みでは、データサイエンスチームの支援を受け、現場の社員が水の使用状況を監視するダッシュボードを作成。同社では8割以上の工場にデジタル技術を学び合うコミュニティがあり、蒸留水の使用状況をモニタリングするアイディア自体も社内でデータ活用事例を共有したことがきっかけで生まれたといいます。こうした「デジタルの民主化」もFactory of the Futureプログラムで目指す姿の1つです。
このほか、在庫適正化ツールの活用やペーパーレス製造・試験の実現、全サイトで進める電子バリデーションの導入など、あらゆる側面でデジタル化が進められています。石丸氏は「AIや自動化、ビッグデータはあくまでツール」と強調。DXで目指すのは無人化ではなく、人が価値の高い創造的で革新的な業務に時間を使えるようにすることだと話しました。